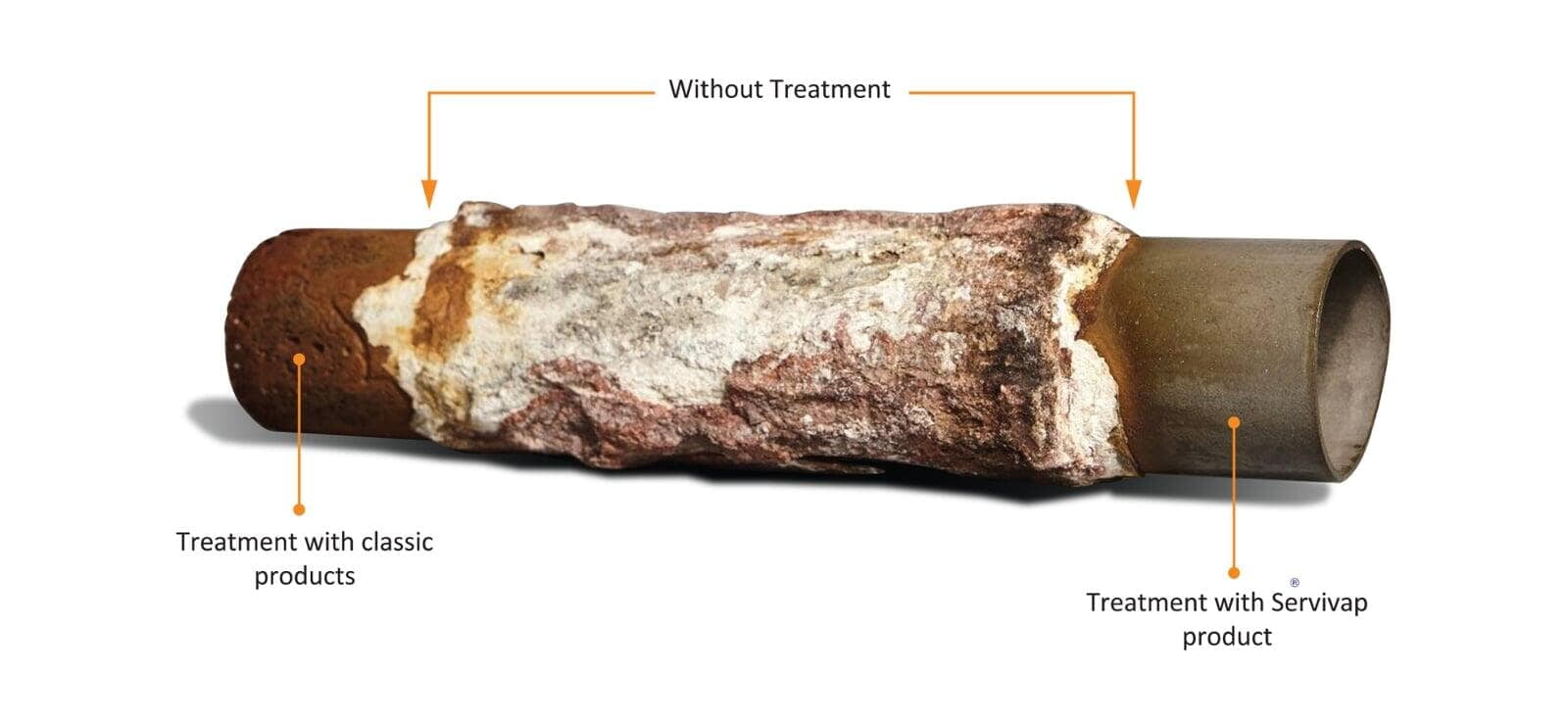
The NEOTANNIN represents a groundbreaking advancement in boiler water treatment technology. Engineered with innovative formulations derived from natural compounds, NEOTANNIN offers unmatched protection against corrosion and scale in steam boilers and closed circuits. Its cutting-edge approach ensures the longevity and reliability of industrial equipment while prioritizing environmental sustainability.
neotannin key's features
- 1 -
Oxygen Scavenger
NEOTANNIN efficiently scavenges oxygen, mitigating corrosion caused by oxidation reactions and prolonging equipment lifespan. This results in reduced maintenance costs and increased operational efficiency.
- 2 -
Scale Inhibition
By stabilizing salts and precipitating minerals, NEOTANNIN effectively prevents the buildup of scale, which can impair boiler efficiency and performance. This leads to a significant reduction in blowdown rates, with potential savings of up to 80% in water consumption.
- 3 -
Silica Dispersant
A common impurity in boiler feed water, can negatively impact boiler performance. Our NEOTANNIN treatment effectively prevents silica buildup on boiler surfaces, safeguarding optimal operation, which is particularly crucial for turbo generators. By switching to NEOTANNIN, silica levels in steam can decrease by 20 to 40%, while maintaining the integrity of key boiler water parameters.
- 4 -
Dynamic Film Formation
NEOTANNIN forms a dynamic, homogenous film on metal surfaces, providing exceptional protection against corrosion even in high-pressure and high-temperature environments typical of steam boilers.
- 5 -
On-line Cleaner
NEOTANNIN acts an online cleaner feature, aiding in the removal of deposits and scale buildup in water systems.
Comparison between Classic chemicals (Sulphites, Phosphates, film forming amines ex. cetamine) NEOTANNIN
The injection of Phosphates, Polyphosphates and Sulphites induces:
● The formation of Calcium Phosphate (Ca3(PO4)2) and the build-up of Calcium Phosphate deposits on the metal surface.
● A limited stabilization of natural salts (Chlorides, Hardness…), requiring higher Blowdown to maintain reduced TDS levels of 2,000-3,500 ppm
● An additional salinity increase (conductivity) in the boiler water due to the inorganic (“salty”) character of these products.
Additional Conductivity generated from Sodium Phosphate / Sodium Sulphite
Na3PO4 + H20 → 3Na+ +PO43-+ H20 → Na2HPO4+ NaOH (NaOH increase pH & Conductivity)
Na2SO3 + H20 → 2Na+ +SO32-+ H20 → SO2 + 2 NaOH (NaOH increase pH & Conductivity)
3 Ca(HCO3)2 + 2 Na3PO4→ Ca3(PO4)2 + 6 CO2 + 6 NaOH (NaOH increase pH & Conductivity)
The above reactions show why it is not reasonable to increase the Conductivity by using Sulphites or Phosphates and you have to maintain the TDS below 3000 ppm. If the TDS reaches a high level, the pH will increase and caustic soda attack may occur, with foaming leading to carryover. Scale may form on the metal surface which will inhibit the heat transfer.
● Adding TDS to the feedwater which reduces the COC (cycles of concentration).
● Increase the blowdown rate to avoid the above problems.
● High fuel and water consumption because of the high level of blowdown.
● Not suitable for low temperature of the feedwater. This will require a higher dosage of Sulphites, adding more TDS and reducing the COC. Increase of the blowdown will increase the fuel consumption and the treatment budget.
Consequences of the injection of filming Amines in boiler water:
● If the pressure exceeds 20 bar, some amines can polymerize on the metal surface and the film will not be effective. Those amines work only for the low and medium pressure boilers.
● Film forming amines require a minimum return condensate of 60%.
● Very expensive treatment.
● If overdosed, a “non-dynamic” film is formed (this film settles by attaching itself to the metal and the film composition is not monomolecular).
● A buildup of Amine molecules creates multi-layer films, which reduce thermic exchanges and causes corrosion underneath the film).
● The film is not an oxygen scavenger.
● The filming amines molecules do not remove existing corrosion or scale on the metal.
Classic (non-purified) tannin treatment (“old school”):
● Classic tannins do not form a closed film on the metal, especially on weld points the protective layer is incomplete or missing.
● Classic tannins contain volatile impurities, which can later form deposits in the condensate system and on steam turbines.
● Classic tannins are much less performant Oxygen scavengers and scale inhibitors. dispersants, pH stabilizers,
● Cleaning of the boiler “on duty” (during the operation, without shutdown) is not possible due to the impurities.
NEOTANNIN TREATMENT
● NEOTANNINs are Oxygen scavengers, Film forming, scale inhibitors, dispersants, pH stabilizers, Cleaners for the boiler during the operation.
● NEOTANNINs do not add TDS to the water, permitting to increase the COC and to decrease the blowdown.
● NEOTANNINs have a dual corrosion protection mechanism since they do not only remove the dissolved Oxygen from the water but also form an Oxygen scavenging, corrosion resistant dynamic Tannate film on the boiler steel.
● NEOTANNINs Inhibit scaling phenomena by stabilization of lime scale cations (Ca++, Mg++) by creating calcium Tannate or magnesium Tannate.
● NEOTANNINs are acting as a dispersant by solubilizing the Tannate of calcium or magnesium.
● NEOTANNINs allow boilers to operate in a range of 8,000 to 12,000 µS/cm (conductivity), cutting blowdown volume without causing carryover of contaminants into the steam.
● NEOTANNINs dynamic film “rejects” the silica and the scale molecules before attaching the metal surface.
● NEOTANNINs natural brown color helps to detect the quality of the treatment, and regarding the iron analysis, SERVIVAP developed a protocol to analyze the iron.
● NEOTANNINs are particularly suitable for low or variable feed water temperatures and very good at protecting idle and intermittently used boilers.
After implementing our NEOTANNIN treatment program
Boiler blowdown can be reduced up to 80%, resulting in annual energy and water savings.
A mere 3-4% reduction in boiler blowdown can save you 1% of your annual fuel costs.
Furthermore, a mere 1 mm deposit of calcium carbonate scale can lead to a significant 7 to 10% reduction in energy efficiency.
PRODUCT ADD-VALUE GUARANTEED
SAVING CALCULATOR
Exploration the financial and operational advantages of NEOTANNIN treatment, such as decreased blowdown, energy conservation, and enhanced boiler efficiency."Utilize our online savings calculator for both technical and financial analyses, including carbon footprint data."